|
Tapes, strips and bars in joints do nothing in joints properly formed to BS 8007.
Neither can they perform a miracle if the workforce chucks them or the concrete in any old how.
A good tape or strip will only overcome slightly poor workmanship - the odd mistake.
As a precaution they have their place.
But they are very difficult to fix down properly, protect from damage, keep dry and keep clean. And the concrete either side has to be sound for a joint not to leak.
|
|
If you specify a tape or a strip without supervision there is a likelihood that the workforce will chuck it and the concrete in leaving voids inches away from the tape where it cannot do any good. If the kicker beneath the tape leaks or the bottom of the wall concrete is honeycombed you still have a leak even if the tape works.
|
Without supervision joints leak.
|
|
|
|
|
Please note. The author acknowledges all the trademarks it mentions on this site.
|
|
|
|
The best of a bad bunch, in my opinion is this product: Fradiflex metal water stop from Max Frank.
Fradiflex has two wide peel off tapes. After fixing it to the top mesh and just before you concrete you peel off the bottom tape to expose the painted surface that the concrete bonds to.
Then at the last moment before your wall formwork goes up you peel off the top tape so that the wall concrete will bind to the steel strip as well.
Clearly unaffected by any rain, unlike anything hydrophylic that will swell early and ruin.
Kept clean for most of the time and still cleanable after that.
Continuous.
Does not fold over when the concrete goes in like rubber waterstops tend to, as well as being far less labour intensive.
But it has to be used properly. Ends lapped as they should be. None missing.
|
|
|
But much better, because they are cheaper and easier
Joints to BS 8007.
The Standard expects the joint to be Properly Made.
What is properly made? More from BS 8007:1987:
The surface of the first pour should be roughened to increase bond strength and provide aggregate interlock
Care should be taken to ensure that the joint surface is clean
Particular care should be taken to ensure that the new concrete close to the joint has an adequate fines content and is fully compacted.
1. Aggregate interlock.
The surface to be bonded to needs to be scabbled.
This concrete was sprayed with retarder an hour or so after the concrete was laid.
It was washed off with a jet wash before the men left that day.
|
|
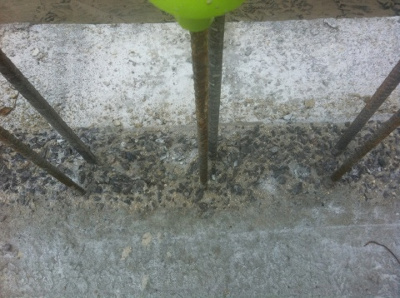 |
This is a mechanical scabbling tool powered by an air compressor.
The problem, compared to spraying retarder and washing it off, is that this tool cannot get under obstructions.
However it will still work if the concrete has been left to harden a day, a month or a year.
You can see that a wide, continuous strip has had all the surface removed and blown clean with the air compressor.
32m of perimeter took less than 2 hours to scabble properly.
Creating aggregate interlock is easy with a bit of planning.
|
|
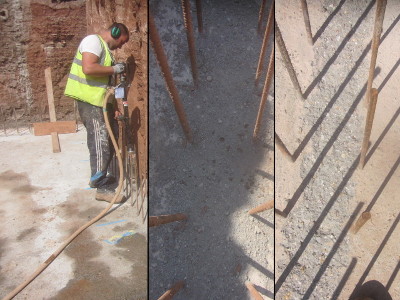 |
|
2. Cleaning.
Having cleaned the surface, it has to be kept clean. My advice is a thoroughly good blow out with an air compressor every day. When you have wall formwork covering the joint, make provision for the dirt to escape through a hole you can patch over.
3. Adequate fines.
That means delivering the concrete to the bottom properly and compacting it properly as well.
If concrete is released from the pump at the top of a 3m high wall it crashes past every horizontal reinforcing bar spraying everywhere inside.
The first concrete delivered loses cement and water to the inside faces of the formwork and the stones fall to the bottom without enough slurry around them.
That's all that it took to create this problem.
|
|
|
|
Concrete is not delivered to site like this.
Rice Crispies / honeycombing at the bottom is something the workforce created.
It is simply and only poor workmanship.
|
|
If you use these 2 simple remedies you should never get honeycombing again.
|
1. Fit a narrower pipe to the pump and lower it most of the way down inside the wall so that concrete freefalls no more than 1250mm. (You may need smaller aggregate to prevent blockages.)
Use the pipe to direct the concrete safely past the steel.
|
|
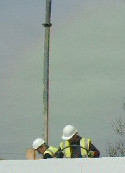 |
|
2. Only form and pour walls to half height at a time.
It isn't really any more labour intensive, firstly because forming half height takes half as long, and secondly because you will have so much less concrete to repair afterwards.
Half height formwork means it is far easier to get concrete to the bottom properly.
It is also far easier to get the poker to the bottom easily. Any more than 2m deep and a poker is curling and getting knotted up in the steel - instead of compacting the lowest layers.
You might not need to buy or hire as much formwork either.
|
|
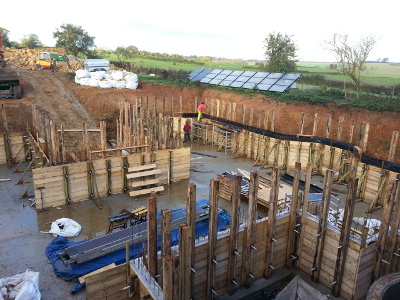 |
|
3. Reinforcing steel sufficient to control cracking.
There need to be enough starter bars through the joint to control cracking when one element cools against the other.
In our experience 0.35% is enough usually. This might be two rows of 16mm bar on 200mm centres through the joint with a 300mm thick wall.
|
|